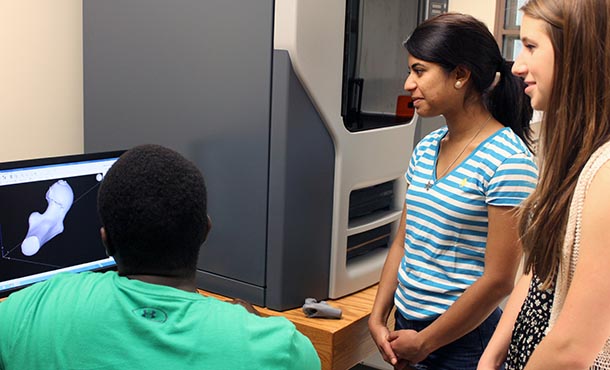
David Wagura, Brinda Shah and Christina Merritt display the image of the head of the human femur that they prototyped using a 3D printer.
Students use 3D printing to create products for medical and household use
Industrial engineering students create prototypes for everything from toothpaste squeezers to human bones
5/8/2015
UNIVERSITY PARK, Pa. — Industrial engineering students Mike Frost and Sean Woodrow knew they wanted to improve the design of an existing product–settling on a toothpaste tube squeezer–when tasked with a class assignment to use reverse engineering and/or 3D printing to design and prototype a product. Meanwhile, Christina Merritt, Brinda Shah and David Wagura chose to focus on creating a prototype that would assist medical professionals–printing a 3D model of a human femur bone.
“We knew we wanted to focus on a consumer product that would improve just one aspect of daily life,” said Frost, a junior from Bethel Park, Pennsylvania.
The prototype Frost and Woodrow designed to save money and the sanity of millions of people around the world? An improved toothpaste tube squeezer that can be used on both regular- and travel-size tubes, allowing users to get the most out of their dental care investment. The design even includes finger rests for comfort.
It may sound simple but the technologies, processes and research behind this type of engineering are extensive and form the basis of the concepts covered in I E 307: Additive Manufacturing Processes and Reverse Engineering.
“New technologies such as additive manufacturing, rapid tooling and reverse engineering are making it possible for companies to significantly cut design and manufacturing cycle times,” said Sanjay Joshi, the instructor of the course. “Our students are exploring these technologies while learning about the basic underlying science behind using these new approaches to design and manufacturing.”
The role of 3D printing (or additive manufacturing) in the design and manufacturing cycle of products and applications in consumer products, medicine, aerospace and other industries is increasing. The industrial engineering program at Penn State is ensuring that students receive a strong foundational understanding of the tools and technologies for additive manufacturing and reverse manufacturing systems as well as the operating principles and characteristics of this type of engineering before they join the workforce.
Some of the advantages for companies that implement additive manufacturing into their processes include: greater design freedom allowing for products to be designed for function; light weighting of structural components; easier mass customization of a product; cost-effective production of small lots; and improved logistics and support.
To begin their project, Frost and Woodrow used reverse engineering, the process of extracting design information from a man-made product and reproducing it, to study a toothpaste squeezer already available on the market.
They found that the internal geometry of the product was too difficult to scan using the 3D scanner in the Reverse Engineering Lab so they had to change their approach.
Their solution was to create a new computer-aided design model from scratch. Once the team had its design completed and loaded into the software, it took less than an hour to print on the 3D printer.
“We learned about the properties of different types of materials and hands-on manufacturing techniques that can translate into other areas of manufacturing,” said Woodrow, a senior from McMurray, Pennsylvania. “With this knowledge, we’ll be able to identify the best materials and processes for creating products when we move into our careers.”
The design team of Merritt, Shah and Wagura took a different approach to the project.
“We wanted to create something that would be beneficial in the health care environment,” said Shah, a senior from King of Prussia, Pennsylvania.
The design team used 2D MRI scans of the head of a human femur and printed a 3D model of the bone.
“The 3D model can be used as a training tool for medical professionals when they explain procedures to patients,” said Wagura, a senior Schreyer Scholar from Broomall, Pennsylvania. “It would be created using the patient’s MRI scans so it would detail the patient’s actual bone structure and any deformities or abnormalities that may be present rather than using a generic model of the bone that is often used in doctor’s offices.”
The team said that the 3D-printed bone also has the potential to be used in implant procedures as the technology continues to evolve and improve as it functions well in the human tissue environment.
“We learned that there are so many software programs that can be used in 3D printing and that most of the work that goes into the process is not the printing itself, but rather getting the data into a workable file that is compatible for printing,” said Merritt, a senior from Cranberry, Pennsylvania.
The team members stated that the class has provided them with a solid foundation of knowledge that they will be able to bring to industry and manufacturing processes once they enter the workforce.
“3D printing is becoming mainstream and now that we have a strong base of knowledge, it will give us an advantage as the technology evolves and expands,” said Wagura.